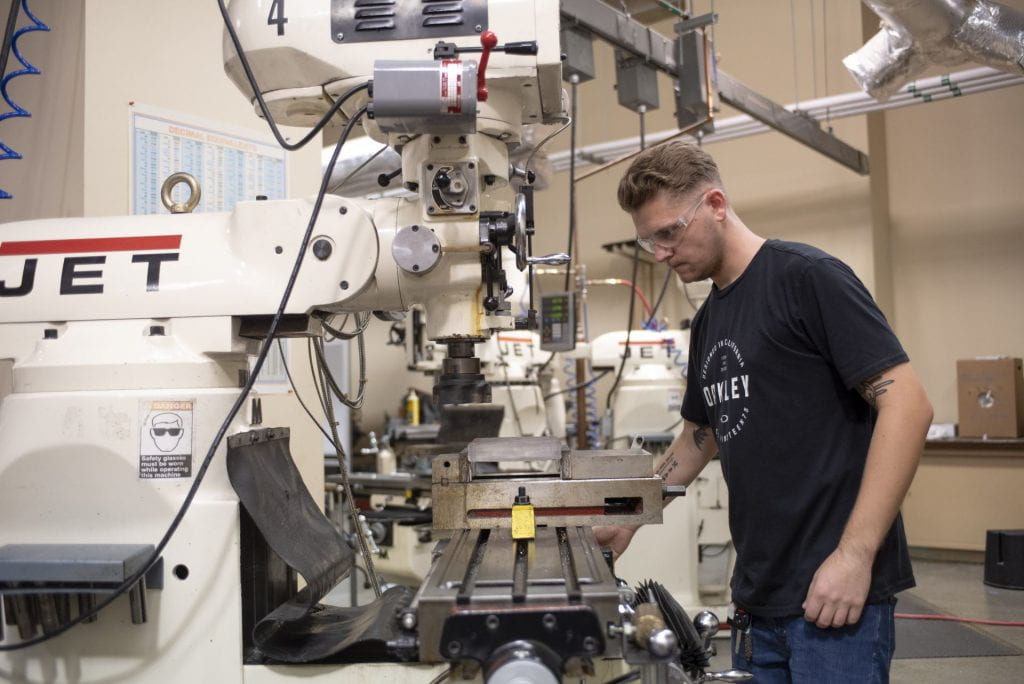
The metal casting industry is energy-intensive with a major portion of the energy used by foundries consumed in melting and holding operations[1, 2]. Significant reductions in energy consumption and environmental impacts are possible with improved melting practice. Foundry melt practices–particularly in small and medium sized foundries–are primarily determined from prior operational experience with differences in practice from operation to operation and even shift to shift. At the same time, there has recently been an increased interest among metal casters in smart manufacturing with its promise of greater resilience and sustainability [3, 4]. However, foundry equipment is designed to operate for many years, and small and medium sized foundries with limited resources often operate with older, analog equipment. However, the availability of inexpensive sensors and the Internet of Things make smart manufacturing principles available to all foundries, even those with older analog equipment[5].
The objective of this project is to use smart manufacturing concepts in the foundry (smart foundry) to improve melting efficiency and monitoring. In this project, internet-connected sensors, Ignition supervisory control and data acquisition (SCADA) software, and cloud storage will be used to provide a power monitoring system for a 125 kW induction melting furnace at Texas State University. This system will be used to measure power consumption and losses during melting with a variety of melt practices to determine practices leading to more efficient and environmentally sustainable operations. The improvements made possible by smart foundry interventions will be evaluated using the cost of conserving energy (CCE) metric[6].
Dr. Trueba leads this project.
[1] W. Liu, T. Peng, R. Tang, Y. Umeda, and L. Hu, “An Internet of Things-enabled model-based approach to improving the energy efficiency of aluminum die casting processes,” Energy, vol. 202, p. 117716, 2020/07// 2020.
[2] E. Pagone, K. Salonitis, and M. Jolly, “Energy and material efficiency metrics in foundries,” Procedia Manufacturing, vol. 21, pp. 421-428, 2018 2018.
[3] A. Sata and B. Ravi, “Foundry Data Analytics to Identify Critical Parameters Affecting Quality of Investment Castings,” ASCE-ASME J Risk and Uncert in Engrg Sys Part B Mech Engrg, vol. 5, p. 011010, 2019/03/01/ 2019.
[4] B. Ravi, “SMART Foundry 2020,” IEEE Potentials, vol. 35, pp. 29-32, 2016/07// 2016.
[5] R. S. Barot, H. Patel, R. Devmurari, K. Shah, B. Sharma, and J. Shah, “IoT feasibility aspects of mold temperature monitoring and casting simulation for smart foundry,” Materials Today: Proceedings, vol. 28, pp. 1732-1738, 2020/01/01/ 2020.
[6] S. D. Supekar, D. J. Graziano, M. E. Riddle, S. U. Nimbalkar, S. Das, A. Shehabi, et al., “A Framework for Quantifying Energy and Productivity Benefits of Smart Manufacturing Technologies,” Procedia CIRP, vol. 80, pp. 699-704, 2019 2019.